硬质合金粉末伺服成型机在数控刀片、刀具、钻头中的应用
鑫台铭硬质合金粉末伺服成型机在数控刀片、刀具、钻头中的应用:---鑫台铭提供。鑫台铭---新智造走向世界!致力于3C电子、新能源、新材料产品成型及生产工艺解决方案。
粉末伺服成型机是一种先进的粉末成型设备,采用机、电、气、仪一体化控制、伺服驱动技术,通过伺服马达带动丝杆转动上冲、母模、下冲进行上下运动的粉末成型机。设备有独立的伺服系统和电气系统,具有浮动压制,精确控制压力和位移,实现了对精细粉末的高精度成型。设备智能精准、可配机械手、自动送粉+摆料。具有高产能、效果好、稼动率高等特点。
粉末伺服成型机主要应用于硬质合金、粉末冶金、精密陶瓷、电子陶瓷、陶瓷结构件、电感磁芯、T-Core电感、铜铁共烧电感、电感一体成型、磁性材料、磁环、铁氧体、铁硅铝、玻璃、铁基合金等粉末材料的压制成型。产品应用于电感、半导体、通讯基站、变压器、电源、3C电子、医疗、数控刀具、电动汽车、新能源(光伏、储能、风电)等领域。
一、设备压力:10T~1200T;
二、驱动方式:
1、上冲(伺服液压缸驱动)+下冲(伺服液压缸驱动);
2、上冲(伺服液压缸驱动)+下冲(AC 伺服马达+丝杆直连驱动);
3、上冲(AC 伺服马达+丝杆直连驱动)+下冲(AC 伺服马达+丝杆直连驱动);
三、模架结构:上一下一、上一下二、上一下三、上二下二、上二下三、上二下四;
四、精度要求:成型精度:≤0.02mm;重复精度:≤0.005mm
硬质合金粉末伺服成型机在数控刀片、刀具及钻头的制造中扮演了关键角色,其高精度、灵活性和智能化特性能够满足现代制造业对刀具性能、效率和复杂结构的严苛要求。以下是其在具体应用中的技术解析与优势体现:
一、核心技术与优势
高动态伺服控制
采用伺服电机驱动,实现压力、速度和位置的毫秒级动态调控,确保粉末填充均匀性和成型密度一致性(密度波动≤0.5%)。
适用于超硬材料(如碳化钨-钴合金)的精密压制,减少烧结后变形。
复杂几何成型能力
通过多轴联动模具设计,可一次成型数控刀片的断屑槽、钻头的螺旋排屑槽等复杂结构,减少后加工工序。
智能化参数适配
结合材料数据库和AI算法,自动优化压制曲线,适配不同刀具的尺寸、形状及材料配比(如梯度硬质合金)。
二、在数控刀片、刀具及钻头中的具体应用
1. 数控刀片(车削、铣削刀片)
需求特点:
刀片需具备高硬度(HRA≥92)、耐高温(>1000℃)和复杂刃型(如负前角、三维断屑槽)。
批量生产要求高一致性(尺寸公差±0.02mm)。
应用方案:
梯度压制:通过伺服压机对刀片不同区域施加差异压力,实现刃口高密度(14.5-15.0g/cm³)、基体适度疏松的梯度结构,提升抗崩刃性。
复杂槽型成型:直接压制出三维断屑槽(如“V”型槽、鱼鳞槽),减少后续磨削成本(节省30%以上)。
涂层适配性:成型坯体表面光洁度高(Ra≤0.8μm),提升CVD/PVD涂层的附着力。
2. 整体硬质合金刀具(铣刀、铰刀等)
需求特点:
长径比大的刀具(如深孔铣刀)需保证高刚性,避免切削振动;微型刀具(如PCB铣刀)需超精密成型。
应用方案:
螺旋刃成型:通过伺服系统控制模具旋转与下压同步,直接压制出螺旋刃(螺距精度±0.05mm),提升排屑效率。
微细结构加工:支持直径0.1mm以下微型刀具的成型,压制力波动<1%,避免刃口微裂纹。
3. 硬质合金钻头(麻花钻、微孔钻)
需求特点:
钻头需兼具高耐磨性和韧性,螺旋槽形状直接影响排屑性能;微型钻头(如PCB微钻)要求极高尺寸精度(直径误差<5μm)。
应用方案:
螺旋槽精密成型:伺服压机通过多工位分步压制,精确控制钻芯厚度与螺旋角(±0.5°),减少钻孔偏摆。
纳米级振动抑制:采用闭环反馈控制,消除压制过程中的机械振动,确保微钻芯部密度均匀(孔隙率<0.1%)。
复合结构钻尖:一次性压制出自定心钻尖(如140°顶角+横刃修磨),提升钻孔定位精度和寿命。
三、实际生产效益
粉末伺服成型机:
成型精度(尺寸公差)---±0.01mm---精度提升80%
密度均匀性---99%-99.5%---烧结变形率降低40%
复杂结构成型能力---近净成型(一次完成)---加工周期缩短50%
能耗效率---按需调节(节能30%-50%)---吨耗电降低40%
提高生产效率
自动化程度高:该成型机能够自动完成粉末填充、压制、脱模等一系列动作,减少了人工干预,显著提高了生产效率。例如,一些先进的伺服粉末成型机可以实现一人操控多台设备,大大提高了单位时间内的产量。
快速成型:伺服电机驱动的传动系统具有较高的响应速度和加速度,使得成型机的压制速度比传统的液压成型机更快,能够在短时间内完成大量产品的生产。
可连续作业:设备稳定性好,可以长时间连续运行,减少了因设备故障或维护导致的停机时间,进一步提高了生产效率。
提升产品精度
精确控制压力和位移:伺服粉末成型机通过伺服电机和精密的控制系统,能够对压力和位移进行精确的控制,保证了数控刀片、刀具和钻头等产品的尺寸精度和形状精度。例如,在生产高精度的钻头时,伺服粉末成型机可以将误差控制在极小的范围内,确保钻头的直径、长度等尺寸精度符合要求。
模具定位精准:采用先进的模具定位系统,如3R定位系统,能够快速、准确地安装和更换模具,并且保证模具在生产过程中的位置精度,从而提高了产品的一致性和精度。
密度均匀性好:在压制过程中,伺服粉末成型机能够使粉末均匀地受力,从而使成型件的密度更加均匀,避免了因密度不均匀导致的产品性能差异。这对于数控刀片、刀具和钻头等对材料性能要求较高的产品来说尤为重要。
优化产品性能
材料利用率高:伺服粉末成型机可以根据产品的尺寸和形状要求,精确地控制粉末的用量,减少了材料的浪费,提高了材料利用率。这不仅降低了生产成本,还有助于节约资源。
微观结构均匀:由于成型过程中压力和温度的精确控制,使得数控刀片、刀具和钻头等产品的微观结构更加均匀,从而提高了产品的硬度、强度、韧性等性能。例如,在生产硬质合金刀具时,伺服粉末成型机可以使合金中的碳化物颗粒分布更加均匀,提高了刀具的切削性能和耐磨性。
可制造复杂形状产品:该成型机具有较好的灵活性,能够生产各种形状复杂的数控刀片、刀具和钻头等产品。通过编程和模具设计,可以实现不同形状和尺寸的产品生产,满足市场的多样化需求。
降低生产成本
减少废料产生:高精度的控制和良好的材料利用率,使得生产过程中产生的废料大大减少,降低了原材料的成本。
降低能耗:伺服粉末成型机在非工作状态下能耗较低,且由于其高效的生产能力,单位产品的能耗也相对较低,从而降低了能源成本。
提高设备利用率:设备的高效性和稳定性,使得设备的利用率提高,减少了设备闲置时间和维修成本,进一步降低了生产成本。
推动产业升级
促进技术创新:硬质合金粉末伺服成型机的应用推动了数控刀片、刀具和钻头等行业的技术创新,促使企业不断研发新的产品和工艺,提高了行业的整体技术水平。
适应市场需求变化:随着市场对高性能、高精度数控刀片、刀具和钻头的需求不断增加,伺服粉末成型机能够满足这些需求,帮助企业更好地适应市场变化,提高市场竞争力。
提升产品质量稳定性:通过精确的控制和稳定的生产过程,伺服粉末成型机能够保证产品质量的稳定性,减少次品率,提高企业的信誉度和市场份额。
四、行业典型案例
数控刀片批量制造
场景:汽车发动机缸体加工用涂层刀片(材质:WC-10%Co)。
方案:伺服压机实现每分钟60片的高速压制,刀片刃口密度梯度控制(表层15.2g/cm³,芯部14.8g/cm³),涂层后寿命达120分钟(传统工艺仅80分钟)。
PCB微钻生产
场景:直径0.2mm硬质合金PCB钻头,用于5G电路板钻孔。
方案:伺服压机纳米级定位+真空除气工艺,钻头直线度<0.005mm/25mm,钻孔10万次无崩刃。
航空钛合金铣刀
场景:钛合金整体叶盘加工用球头铣刀(直径12mm,4刃)。
方案:伺服成型直接压制螺旋刃+球头轮廓,刃口跳动<0.01mm,刀具寿命提升50%。
五、未来技术趋势
超精密成型:开发亚微米级定位精度的伺服系统,支持纳米硬质合金刀具(如MEMS加工刀具)制造。
多材料复合压制:在同一刀具中集成硬质合金(刃部)与钢基体(刀柄),实现“一步成型”。
数字孪生集成:通过虚拟仿真实时优化压制参数,减少试模次数(目标:新刀具开发周期缩短70%)。
总结
硬质合金粉末伺服成型机通过高精度动态控制与智能化工艺,为数控刀片、刀具及钻头提供了复杂结构近净成型、梯度材料适配和微细加工能力的核心解决方案,显著提升了刀具的切削性能、寿命及生产效率。在高端制造(如航空航天、3C电子)领域,其技术优势正推动硬质合金刀具向超精密化、功能集成化方向快速发展。
综上所述,硬质合金粉末伺服成型机在数控刀片、刀具及钻头制造领域展现出了显著的优势,不仅提升了生产效率与产品精度,还优化了产品性能并降低了生产成本,为产业的升级与发展注入了强大动力。
相关资讯
推荐产品
最新资讯 News
联系我们 Contact Us
-
联系人:刘大军
手 机:18138436465
电 话:0755-28365643
传 真:0755-89636058
邮 箱:33434175@qq.com
地 址:深圳市龙岗区坪地街道六联社区鹅公岭西路6-12号
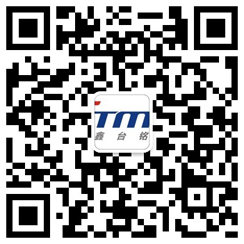